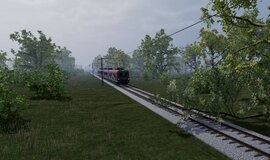
Fully automated, driverless driving:
Simulation-based tests in the laboratory avoid expensive field tests
The development of fully automated, driverless driving in rail networks requires a large number of tests. It must be proven that the control system functions reliably and safely under all possible operating conditions (e.g. passing a construction site) and environmental conditions (e.g. day/night, fog, rain, snow). In addition, sensor systems for object and environment detection are used for track monitoring, which increases the complexity of the test. However, field tests in the rail sector are considerably more difficult to carry out than in the automotive industry, where larger vehicle fleets can be deployed comparatively easily. The availability of tracks and trains is limited. Efficient test strategies are therefore necessary in order to reduce expensive and time-consuming field tests to the unavoidable minimum.
A fully automated train (Automated Train Operation, Grade of Automation Level 4 - ATO GoA 4) takes over almost all preparatory and final steps independently in addition to the journey. Instead of a train driver, the train is controlled by various new onboard systems, which in turn use powerful sensor systems for object and environment recognition. As a rule, these new systems have additional interfaces to a train control and management system (Traffic Control Management System - TCMS) and to the ETCS onboard system. The interaction of all systems involved must be verified in numerous tests. In order to reduce the time-consuming and expensive field tests required for this, intelligent test environments are being developed that enable as many tests as possible to be carried out in the “laboratory”.
These test environments allow system integration, verification and validation tests in all development phases. Digitale Schiene Deutschland has installed corresponding test environments in its test field at the Havelländische Eisenbahn (HVLE) in Berlin-Spandau. Comparable approaches are also used in the automotive industry for highly or fully automated systems. The illustration provides an overview of the test environments used.
With the test environments, all tests in the early development phases can be carried out entirely in the laboratory. Only in later phases are targeted field tests carried out on tracks. The first step, “Model-in-the-Loop” (MIL), can be started right from the beginning, in the system requirements phase. With advanced system development, the steps “Software-in-the-Loop” (SIL), “Hardware-in-the-Loop” (HIL), “Testing in the test field” and “Data Replay” are then introduced. Only in the final phase of the project, when the system to be tested (system under test, SUT) is fully developed, are more cost-intensive field tests implemented.
Digitale Schiene Deutschland is testing these approaches in the AutomatedTrain development project, which is funded by the BMWK. Together with nine partners, it is demonstrating a fully automated, driverless dispatching and stabling as well as the associated automated train preparation and shutdown.
In the current issue of Signal & Draht magazine (11/24), the test strategy, the test phases and the individual test environments required for the development of fully automated driving are described in detail.