
Digital Impact Detection in Railway Operations
Collecting data for driverless driving – a ride with the advanced TrainLab
Berlin, May 2024 - When trains run driverless in the future, they will not only have to keep an eye on the track, but also be able to independently assess impact events. Digitale Schiene Deutschland is therefore involved in the funding project "KI-Methoden in der Zustandsüberwachung und bedarfsangepassten Instandhaltung von Schienenfahrzeugstrukturen" (KI-MeZIS). The aim of the project is to develop the potential of artificial intelligence for monitoring such events. To this end, data is collected, analysed and interpreted during test runs throughout Germany. In this interview, network coordinator and subproject manager Dr Martin Köppel explains how the data is detected and what is important when collecting data.
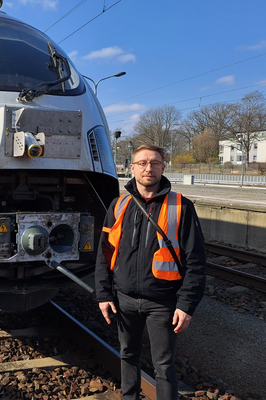
"The data collection for today's journey is focussed on normal operation," says Martin Köppel. "The aim is to record a train journey without any incidents. The data will later serve as a basis for comparing recordings of actual impact tests."
On a sunny spring day in March, Deutsche Bahn's advanced TrainLab (aTL) started one of its numerous test runs in Potsdam. It is the fastest moving laboratory in Germany – an ICE train of the 605 series, which was still in use in passenger transport until 2017 and is equipped with various measurement technologies. The aTL drives on electrified and non-electrified lines and can be used flexibly. It is available to the entire railway industry for test runs and covers a wide range of tests for innovative technologies. These are not possible with regular passenger or freight trains. Employees from Digitale Schiene Deutschland and the project partner IFB – Institut für Bahntechnik were on board for the test drive around Berlin. The network coordinator and subproject manager, Dr Martin Köppel (Digitale Schiene Deutschland), supervised the trip and provided exciting insights into the project.
In addition to the field tests, which are being conducted throughout Germany, laboratory tests were carried out in advance in which parts of the aTL were confronted with impact situations. The project partners, DLR - Deutsches Zentrum für Luft- und Raumfahrt and the University of Stuttgart (Institut für Maschinenelemente, IFM), carried out the tests.
The development of an impact detection system is crucial for Digitale Schiene Deutschland, as unforeseen events, such as a tree or animal on the track, occur more frequently in open networks in the mainline railway sector. Although these events are extremely rare in relation to the train kilometres travelled, they must be taken into account in all their forms during development. In the system architecture of Digitale Schiene Deutschland, impact detection is part of "perception", which is environment detection. It is required for Automatic Train Operation (ATO) at the highest level of automation GoA4 (Grade of Automation 4). This level makes it possible to deploy vehicles more flexibly and more frequently – an important prerequisite for additional traffic and increased capacity on the railway. Measurements are taken using sensors for impact and rollover detection, which are attached to the front and undercarriage of the train. This enables collisions to be detected and conclusions to be drawn about the condition of the vehicle. Artificial intelligence (AI) then analyses and interprets the collected data.
"A simple camera is not sufficient for impact detection, because there is always a so-called blind zone in visual recordings. This means there is a high risk of overlooking something," says Martin Köppel. The impact intensity cannot be measured with a camera either. However, this is necessary in order to determine the extent of the damage caused to the train by a collision. The technology installed in the aTL therefore also includes so-called pressure and accelerometers, strain gauges as well as rotation and pulse sensors. The camera installed in the front area only serves as a "backup" in order to be able to visually reconstruct unclear collision situations afterwards.
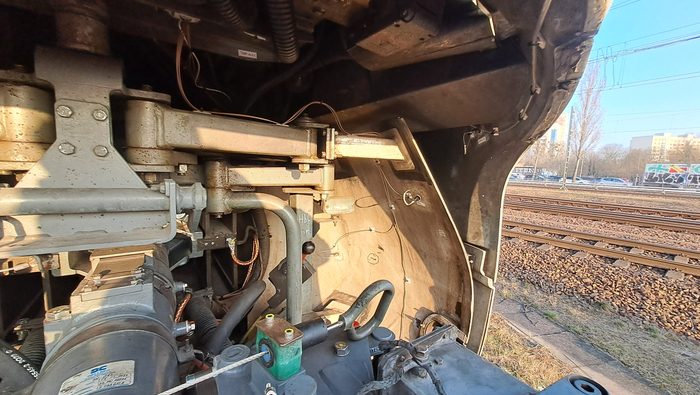
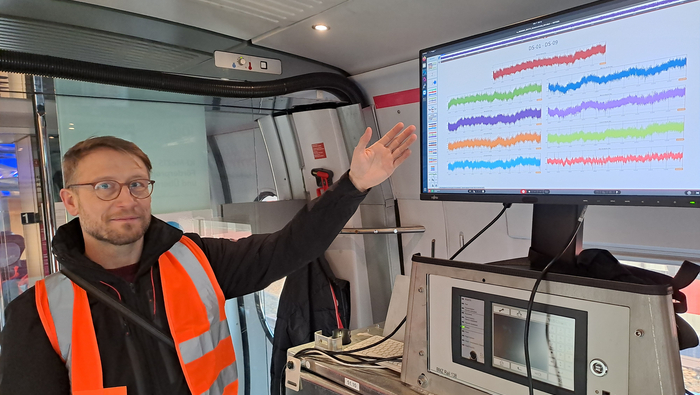
Impact detection system from Digitale Schiene Deutschland differs from competitor products
The system uses the recorded sensor data to determine which safety-relevant steps are required: For example, does the train need to be stopped in the event of a collision, or can it continue to the next station. "These explicit recommendations for action set our system apart from other products on the market," says Martin Köppel. In addition to the test run around Berlin, two more test runs are planned for this year. The laboratory tests have been completed. This also included so-called “Beschussversuche”, in which the front cap of the aTL was "shot at" with various objects at different speeds. Last year, so-called "rollover tests" were also carried out at the Havelländische Eisenbahn (HVLE) in Berlin-Spandau (more information here: link). Among other things, a freight wagon equipped with sensors was used. At speeds of up to 30 km/h, it rolled over various objects such as steel pipes, concrete segments and a shopping trolley. The freight wagon replaced the aTL, as it incurs significantly lower costs in the event of damage. The data collected will also be used for the further course of the project.
Simulations complement real-life tests
However, the data collected in the real-life and laboratory tests is not sufficient to comprehensively train an AI. For this reason, further tests are carried out in digital simulations with virtual impact and rollover events. The real data recorded serves as reference values. "A simulated environment absolutely needs real tests in order to be able to compare the extent to which reality and simulation differ," says Martin Köppel. For the simulations, the underrun protection of the train is generated digitally and superimposed with the data of the real underrun protection. This involves checking whether the measured values are similar in the event of an impact. "With a good simulation, there is only a maximum deviation of 10 per cent," so Köppel. Sufficient data for an AI can only be generated through the supplementary simulation tests.
The data is stored on the servers of Industrial Analytics GmbH and analysed using AI. In addition, the data is collected in a so-called Data Factory. This is a platform that enables railway companies and manufacturers to collect, process and simulate sensor data across Europe and make it available for mutual use. One aim is to create a comprehensive data basis for training AI software. Martin Köppel: "The KI-MeZIS project is currently in the technical development stage TRL 6 (Technology Readiness Level of 1-9) and therefore in the prototype phase". In the long term, the system is to be transferred to other vehicle types and put into regular operation. The necessary measures for this will be coordinated with the project partners involved over the coming months. In any case, sufficient data was collected during the journey around Berlin. "The day's goal was achieved. We are satisfied with the result," says Martin Köppel as the aTL arrived back at Potsdam. The next trip is planned for June –possibly in the rain. After all, factors such as different weather conditions are also crucial for data collection.
KI-MeZIS articles:
Offener Multisensordatensatz für die Entwicklung der Umfeldwahrnehmung beim vollautomatischen Fahren | Eisenbahntechnische Rundschau, April 2023 (only in German)