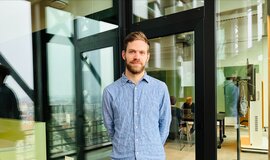
AutomatedTrain: Christian Pfeiffer on the sensor setup for fully automated, driverless dispatching and stabling
The future of fully automated rail transportation is now:
In the AutomatedTrain project, Digitale Schiene Deutschland is working with 8 partners to develop and demonstrate the technical feasibility of fully automated, driverless dispatching and stabling of trains as well as the automated preparation and shutdown of trains. Christian Pfeiffer, Project Manager Perception at Digitale Schiene Deutschland, gives an insight into the environment sensor technology used for obstacle detection in fully automated stabling and dispatching.
Christian, what will the train of the future look like that can travel fully automated and driverless from the stabling area to the track?
With our AutomatedTrain project, we are demonstrating that driverless stabling and dispatching is technically possible. In addition to the automation of various vehicle components, the train of the future needs one central capability in particular: it must be able to independently recognize whether the visible route is free of objects and obstacles.
To achieve this, in AutomatedTrain, a sensor set is installed at the front of the train to detect the surrounding. As part of the project, Siemens Mobility and Bosch Engineering are developing a new obstacle detection system with a joint system approach, which will being integrated into a Mireo train from Siemens Mobility on the one hand and an S-Bahn Stuttgart train, series 430 from Alstom, on the other. The conversion of the vehicles will start in spring 2025. The demonstration of driverless dispatching and stabling takes place with a Mireo vehicle in the Siemens Mobility test and validation centre in Wegberg-Wildenrath. The field tests to collect sensor data and derive actions in real operation will take place on reference routes in Stuttgart.
Which sensors are actually installed?
Our sensor setup for environment perception includes
✅ 6 Lidar sensors for medium and long-range environment detection
✅ 7 color cameras with a high dynamic contrast range for object detection
✅ 3 radar sensors for obstacle detection at close and medium distances
✅ 8 ultrasonic sensors for close-range detection
✅ 2 infrared cameras (LWIR) for detecting heat sources
This combination of different sensor technologies and viewing areas is designed to ensure the most precise and robust detection of the environment possible - a crucial prerequisite for safe driverless operation.
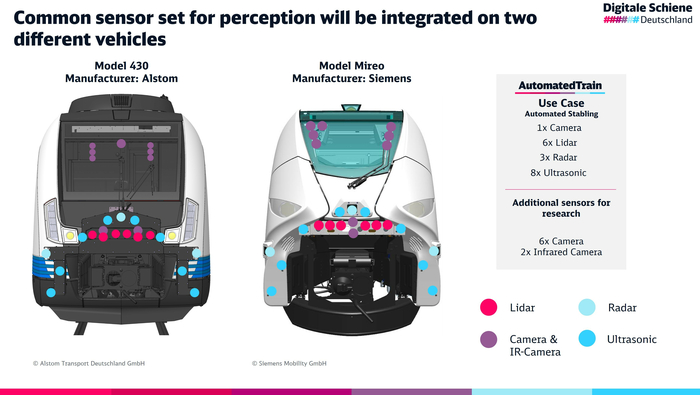
What challenges must sensor technology and environment detection overcome?
A key requirement for such a system is that the sensors and downstream detection algorithms must be at least as powerful as a train driver. This means:
- Predictive obstacle detection: people and objects on the track must be detected at an early stage so that automatic braking can be initiated in good time.
- Reliability under all environmental conditions: Even the most adverse weather conditions such as heavy rain, fog, snow, hail, storms and darkness must not significantly impair sensor performance.
- Integration into existing vehicles: The system must be able to be integrated into different types of trains.
To date, there is no system on the market that attempts to reproduce the perception of a train driver on this scale. We are focusing on a multimodal approach to meet the stringent safety requirements of the rail industry, based on a variety of sensor technologies.
In addition, we have to comply with railway-specific requirements for electromagnetic compatibility (EMC), impact resistance and fire protection, among others, before using them in rail vehicles. Another aspect is the protection of sensors and interfaces against manipulation by third parties.
What are the next steps?
We are currently putting all the sensors into operation in our dynamic mock-ups: a test vehicle representing the BR430 S-Bahn and another representing the Mireo vehicle. These are located at the Havelländische Eisenbahn in Berlin Spandau, where we will be testing the first version of the obstacle detection system over the next few weeks.
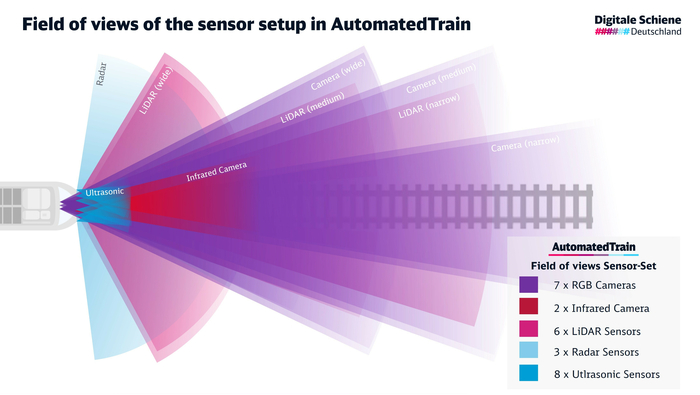
The so-called Vehicle Data Logger is also used here. It records the data collected by the sensors and enables us to provide the same input data at different stages of the system's development. This allows us to evaluate progress and improvements clearly and comparably.
This database also lays the foundation for a scalable solution: in the long term, more and more vehicles can be used as data generators and connected to the so-called Data Factory. In the Data Factory, the sensor data is recorded, stored and processed to generate high-quality multi-sensor data sets and a synchronised multi-sensor data pool. These data sets are essential for the development and improvement of machine learning and enable the training of artificial intelligence that can precisely recognise objects and track conditions to enable fully automated rail operations. This enables the continuous further development of object dectection across project boundaries.
In addition to the technical details, many people are certainly also interested in the practical application of this technology. Will there soon be an opportunity to see the sensor technology and the data infrastructure behind it live?
At the Hannover Messe from March 31 to April 4, 2025, we will be presenting our project at the joint stand of the Industry 4.0 platform. If you would like to find out more, you are cordially invited to visit us there!
With AutomatedTrain, we are driving forward automation on the railways - and setting an important milestone for the rail traffic of the future.
AutomatedTrain is funded by the Federal Republic of Germany and the European Union. Funding is provided by the Federal Ministry for Economic Affairs and Climate Protection on the basis of a decision by the German Bundestag and the European Union.