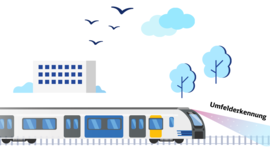
Fully automated, driverless driving: A response to the shortage of skilled labour in the rail industry
Gradual introduction enables the fastest possible benefits
Berlin, May 2024 - Demographic change and the resulting increasing shortage of skilled workers are also leaving their mark on the rail industry. For many railway undertakings (RUs), it is becoming increasingly important to operate trains with fewer staff. Fully automated, driverless driving provides an answer to this. In the target state, technically trained employees will no longer be needed on board a train. However, there are still many challenges to overcome before this is achieved. It therefore makes sense to develop and roll out the system in stages in order to realise benefits as quickly as possible.
Train cancellations due to a lack of staff - especially train drivers (Td) - are unfortunately the rule these days. In North Rhine-Westphalia, for example, five per cent of trains were cancelled at short notice at the beginning of the year. The most common reason for this was a lack of staff. The sharp increase in retirements and the trend towards a reduction in weekly working hours for shift workers will further exacerbate the problem in the future. Fully automated, driverless driving offers a technical solution to this problem. Technically trained personnel, usually with several years of training on board a train, will no longer be necessary. Operations can therefore be maintained with fewer critical personnel.
There are already underground trains and so-called "people movers" around the world that are fully automated. However, these systems are operated in closed networks - either in tunnels, on elevated tracks or on secured routes. This means that no automated systems are required for obstacle detection or route monitoring. In contrast, such systems are mandatory for fully automated operation in open networks.
Fully automated railway operation requires a wide range of modern technology. At the front and side of the train, sensors (radar, Lidar, camera, ultrasound and infrared) take over the function of the human eye. The sensor data generated is fused with other data, such as a highly accurate digital map of the surroundings. Irregular situations are recognised and transmitted to the vehicle control system. Ultimately, the system triggers a reaction fully automatically.
In order to enable the systems to react to their environment, sensor data is recorded in the vehicle in advance and a large number of operationally relevant scenarios are identified and simulated outside the system. All data is stored in a central data centre and in turn made available to the systems to optimise the reaction behaviour (so-called Data factory). Extensive development work still needs to be carried out here. Digitale Schiene Deutschland therefore relies - as far as possible - on the transfer of technologies from other sectors, such as the automotive industry, in order to minimise development costs and increase the speed of development. Further challenges are the legal and operational framework conditions with regard to driverless driving, the realisation of necessary investments by the industry and the integration
Against this backdrop, Digitale Schiene Deutschland is planning a phased introduction of fully automated driving (see diagram). Each stage offers a direct benefit and contributes to the realisation of the ultimate goal of fully driverless driving.
Five stages to the target image
In automatic train operation (ATO), a distinction is made between highly automated driving in automation level 2 (ATO GoA2) and fully automated, driverless driving in automation level 4 (ATO GoA4). In the former mode, the train drives, brakes and stops automatically. Responsibility for safety remains with the driver, who intervenes in the event of irregularities. In automation level 4, safety responsibility lies entirely with the system.
The initial stage is highly automated driving in ATO GoA2 over ETCS mode. This is technically feasible today and has been trialled by Digitale Schiene Deutschland in various projects and is currently being rolled out for the first time in the Stuttgart digital node by 2026. The direct benefits are lower energy consumption, greater operational stability by avoiding manual errors and lower maintenance costs. The driver remains on board.
The next stage will be the automated set-up and provision of the train. To achieve this, numerous vehicle functions, such as the preparation service, which currently requires manual interaction by the driver, must be automated. In addition, safe perception of the surroundings and the ability to react to disruptions at lower speeds must be implemented. The driver no longer has to take care of the preparatory and final service on the vehicle and the planned journey times for this can be eliminated. He or she only boards the train from the first station and then drives the train conventionally in ATO GoA 2 mode. Drivers are no longer required for preparation and could then be deployed on the line, for example.
The next stage will involve fully automated driving with passengers between stations at a higher speed. However, there is still trained staff on board to deal with emergencies and incidents, who can intervene in the system in case of doubt, resolves emergencies and incidents and instructs the evacuation of the train. In the subsequent stage, the trains generally run without any active personnel. Only in the event of a fault or emergency specialised personnel take over remotely to correct faults.
All previous stages have initially focussed on regional and suburban rail transport - among other things due to lower travel speeds and the high demand for travelling personnel. In the final stage, fully automated driving will be transferred to other types of transport, such as rail freight transport, local and long-distance passenger transport. To this end, the respective specifications must be expanded or adapted and realised and tested as part of initial implementations.
Project AutomatedTrain 2023 started
With the AutomatedTrain project launched in summer 2023, Digital Rail Germany is putting an advanced prototype for stage 1 on the rails by 2026. The project is being funded by the Federal Ministry for Economic Affairs and Climate Protection with around EUR 42 million. The aim of the project is to demonstrate the technical feasibility of a fully automated start-up as well as the dispatching and parking functionality with limited speed in open networks under ETCS. The prototype implementation of obstacle detection will be be carried out with a jointly defined sensor set on two different vehicle types.
In our current article in the trade magazine Vollautomatisiertes, fahrerloses Fahren auf der Schiene - Herausforderungen im Bahnsystem | Mai 2024 EI - Der Eisenbahningenieur (EI 05/24) you will find further interesting information on the subject of fully automated driving, the state of the art and current pilot projects.
We hope you enjoy reading it!