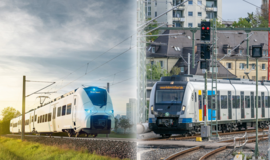
Fully automated, driverless rail operation:
Operating concept and system architecture of the “AutomatedTrain” project
Fully automated, driverless driving offers great opportunities to deploy traction units more flexibly. At the same time, it can also counteract the increasing shortage of skilled workers. However, implementation in the open rail network is technologically challenging. The “AutomatedTrain” project of Digitale Schiene Deutschland has begun to automate dispatching and stabling as well as labor-intensive preparation and shutdown of trains for the first time. An important step towards driverless driving in regular operations. The operating concept has now been developed and the system architecture presented as part of the project.
AutomatedTrain is mainly about automated preparation, the dispatching and stabling and the shutdown of trains. This will significantly reduce the workload of rail operations staff in the future, freeing up personnel capacity. The aim of the project is to demonstrate the technical feasibility of fully automated, driverless driving at the highest level of automation “ATO GoA4” (Grade of Automation 4) in open networks. The implementation is carried out in accordance with the objectives of Digital Rail Germany in an ETCS environment (“ATO over ETCS”) and with on-board environment and obstacle detection. For this purpose, two different multiple units will be equipped with a sensor set for object detection: a Mireo multiple unit from Siemens Mobility and a series 430 multiple unit from Bombardier/Alstom. The demonstration of the driverless standby and parking runs will take place at Siemens Mobility's test and validation center in Wegberg-Wildenrath. The field tests to collect sensor data in real operation will take place on reference routes in Stuttgart and Munich.
The system architecture comprises a central control unit, the so-called “Automatic Processing Module”, which handles communication with the control center and the ETCS, ATO and vehicle control systems on the train. Another central architecture component is the “Object Detection System” for sensor-based environment and obstacle detection. Another component is the “Vehicle Data Logger”, which records all sensor data and forwards it to the “Data Factory”. This data supports the continuous further development of the prototype system and the training of future systems.
The project follows the so-called CENELEC phases for technical certification and aims for a modular architecture that can be flexibly expanded and integrated into both new and existing train types. In this way, “AutomatedTrain” should contribute to the approval of fully automated train control and create a basis for future tenders and European standardization - an important step towards the future of fully automated driving in Europe's open networks.
The operating concept and system architecture of “AutomatedTrain” are explained in more detail in the magazine Deine Bahn (11/2024).
Link to the article (only in German)
Watch a video to find out more about the automated dispatching and stabling of trains and the “AutomatedTrain” project.
Link to the video
*AutomatedTrain is funded by the Federal Republic of Germany and the European Union. Funding is provided by the Federal Ministry for Economic Affairs and Climate Protection on the basis of a resolution of the German Bundestag and the European Union.